Argon arc welding machines ESAB OrigoTig, BuddyTig, etc.
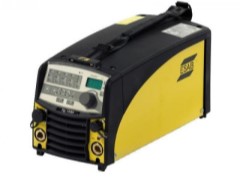
An argon welding machine is an inverter connected to a 220 or 380 V network, which converts the current from alternating to direct several times, while increasing its frequency. Inside, several transformers, diode bridges and a key board are used. All this contributes to a light weight of 4-30 kg and high quality of the seam.
If you need a welding machine in the garage, then choose the 220 V model. For production, 380 V is optimal. The weight of 4-8 kg is useful when traveling and working at height, as well as with three-dimensional structures. With stationary use, weight does not matter.
The TIG method has clear advantages over other welding methods, but working with an argon welding machine also has several disadvantages that you need to be prepared for when choosing this welding method.
Advantages of the TIG method
- local heating eliminates serious deformations of the product;
- a thin tungsten needle allows you to create narrow, neat seams;
- it is possible to weld with and without an additive, affecting the height of the roller;
- the compound is obtained without a slag crust on top;
- in most cases, no follow-up is required.
- mechanical processing;
- stainless steels and non-ferrous metals can be welded;
- the seams are sealed and withstand high pressure;
- there are no splashes of metal sticking to the surface.
Disadvantages of the TIG method
- connection speed is inferior to MIG;
- the burner hood interferes with work in hard-to-reach places;
- the ceramic nozzle slightly limits the visibility of the welding bath;
- the quality of the seam depends on the user's skills (it will not work immediately to take and cook like a semi-automatic machine);
- it is required to constantly feed the additive with the second hand and control its length (during welding, the length of the wire is rapidly reduced, and long pieces are inconvenient to hold in your hands,
- because they "walk");
- tungsten electrodes are more expensive than coated ones;
- additional costs for argon;
- it is impossible to weld parts efficiently on the street in a strong wind (argon is blown away and the welding bath remains unprotected).
Models: Origo Tig 3000 AC/DC, Origo Tig 3001i TA23, Origo Tig 3001iw TA23, Origo Tig 3001i TA24, Origo Tig 3001i TA24 AC/DC, Origo Tig 3001iw TA24, Origo Tig 4300 AC/DC, Buddy Tig 160, Caddy Tig 1500i TA33, Caddy Tig 1500i TA34, Caddy Tig 2200 AC/DC, Caddy Tig 2200i TA33, Caddy Tig 2200i TA33 DC, Caddy Tig 2200iw TA33, Caddy Tig 2200i TA34, Caddy Tig 2200iw TA34, Caddy Tig 2200iw TA34 AC/DC, Aristo Tig 4000iw TA6, Aristo Tig 4000iw TA4, Aristo Tig 4000i TA6, Aristo Tig 4000i TA4.
- Origo Tig 3001iw TA24. Технические характеристики.
- Origo Tig 3001iw TA23. Технические характеристики.
- Origo Tig 3001i TA23. Технические характеристики.
- Caddy Tig 1500i TA33. Технические характеристики.
- Caddy Tig 1500i TA34. Технические характеристики.
- Aristo Tig 4000iw TA6. Технические характеристики.
- Aristo Tig 4000iw TA4. Технические характеристики.
- Caddy Tig 2200i TA33 DC. Технические характеристики.
- Caddy Tig 2200i TA33. Технические характеристики.
- Caddy Tig 2200iw TA33. Технические характеристики.
- Caddy Tig 2200iw TA34. Технические характеристики.
- Caddy Tig 2200i TA34. Технические характеристики.
- Origo Tig 3001i TA24 AC/DC. Технические характеристики.
- Aristo Tig 4000i TA6. Технические характеристики.
- Caddy Tig 2200i TA34 AC/DC. Технические характеристики.
- Origo Tig 4300 AC/DC. Технические характеристики.
- Origo Tig 3000 AC/DC. Технические характеристики.
- Caddy Tig 2200 AC/DC. Технические характеристики.
- Buddy Tig 160. Технические характеристики.
- LHN 200i Plus. Технические характеристики.
- RENEGADE ET 300i/ET 300iP. Технические характеристики.
- RENEGADE ES 300i. Технические характеристики.
- LHN 250i Plus. Технические характеристики.
- Origo Tig 4300iw TA24 AC/DC. Технические характеристики.
- Origo Tig 3000i TA24 AC/DC. Технические характеристики.
- Aristo Tig 4000i TA4. Технические характеристики.
- Origo Tig 3001i TA24. Технические характеристики.
- Caddy Tig 2200iw TA34 AC/DC. Технические характеристики.
All ESAB products
About ESAB
-
The past
ESAB reflects both the rich heritage of design leadership and the historical alliance of several welding industry leaders. In 1989, many leading companies of that time joined together to create a powerful welding alliance. -
Present
ESAB Corporation strives to strengthen the position of world pioneers in the field of world-class manufacturing technologies. Today ESAB is introducing new technologies, reaching new frontiers and writing the history of welding for more than a hundred years. -
Future
ESAB Corporation will continue to innovate for future production technologies and specialty gas solutions to serve as the paradigm of the future for these industries and the industries they serve.
NEW TECHNOLOGIES GROUP
Contact us or your local dealer for more information on certifications, features, reviews, pricing, stock availability and delivery terms for ESAB products.
Reply guaranteed within 8 business hours
- (727)345-47-04
- (3955)60-70-56
- (8182)63-90-72
- (8512)99-46-04
- (3852)73-04-60
- (4722)40-23-64
- (4162)22-76-07
- (4832)59-03-52
- (8352)28-53-07
- (351)202-03-61
- (8202)49-02-64
- (3022)38-34-83
- (395)279-98-46
- (4932)77-34-06
- (3412)26-03-58
- (4012)72-03-81
- (4842)92-23-67
- (843)206-01-48
- (3842)65-04-62
- (4212)92-98-04
- (8332)68-02-04
- (4966)23-41-49
- (4942)77-07-48
- (861)203-40-90
- (391)204-63-61
- (3522)50-90-47
- (4712)77-13-04
- (4742)52-20-81
- (3519)55-03-13
- (375)257-127-884
- (495)268-04-70
- (8152)59-64-93
- (8552)20-53-41
- (831)429-08-12
- (3843)20-46-81
- (383)227-86-73
- (3496)41-32-12
- (3812)21-46-40
- (4862)44-53-42
- (3532)37-68-04
- (8412)22-31-16
- (342)205-81-47
- (8142)55-98-37
- (8112)59-10-37
- (863)308-18-15
- (4912)46-61-64
- (812)309-46-40
- (846)206-03-16
- (8342)22-96-24
- (845)249-38-78
- (8692)22-31-93
- (3652)67-13-56
- (4812)29-41-54
- (862)225-72-31
- (8652)20-65-13
- (3462)77-98-35
- (8212)25-95-17
- (4752)50-40-97
- (998)71-205-18-59
- (8482)63-91-07
- (3822)98-41-53
- (4872)33-79-87
- (4822)63-31-35
- (3452)66-21-18
- (347)229-48-12
- (3012)59-97-51
- (8422)24-23-59
- (8672)28-90-48
- (4922)49-43-18
- (423)249-28-31
- (844)278-03-48
- (8172)26-41-59
- (473)204-51-73
- (4112)23-90-97
- (4852)69-52-93
- (343)384-55-89